レポート#9:1日120分の作業短縮!倉庫の保管業務を改革した自動倉庫の事例紹介
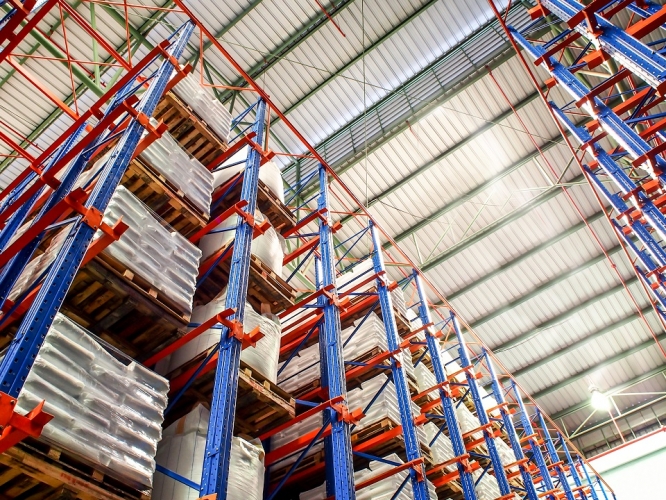
2021年11月11日、「自動倉庫で実現する部品保管改革」を配信しました。今まで人間が行っていた保管業務を「自動倉庫」に統合することで、どのような効果が発揮できるのか?自動倉庫から始める倉庫オペレーション改革を、お客様の事例を交えて第2営業部 副部長の乾氏が紹介しています。
目次
・自動倉庫とは
・自動倉庫の種類
・お客様事例インタビュー
・自動倉庫のメリット・デメリット
・まとめ
自動倉庫とは
はじめに、乾氏は自動倉庫とはどのようなものか説明しています。
自動倉庫は、製品の受け入れから保管、出庫までの一連の流れをコンピューターで一元管理するオートメーションシステムを導入した倉庫です。続けて、乾氏は自動倉庫の特徴について「棚を天井高くまで設置して、取り出しをスタッカークレーンと言われるリフトのようなもので、すべて自動で行う設備」と話します。
自動倉庫の種類
次に、自動倉庫の種類について紹介しています。
種類は、大きく分けて自動ラック、移動ラック、回転ラックの3種類です。
・自動ラック
パレット単位の製品や部品を自動搬送し、天井高くまで設置された高層ラックに保管するタイプ。パレットのほかにも、バケットタイプやコンテナやダンボール、トレイなどの形状や重量にとらわれず収納できるフリーサイズのタイプがあります。
・移動ラック
棚そのものを移動台車に載せて、密集保管を可能にする電動式タイプ。棚自体が移動するため、倉庫内のスペースを最大限に有効活用でき、保管効率やピッキング効率を向上させます。
・回転ラック
高さ方向を有効活用したタイプ。縦に棚を設置して、回転させることで省スペース化を実現します。
その他に、2つのタイプがあります。
・傾斜式流動ラック
水平に搬送して保管するタイプ。棚には傾斜角度がついていて、保管側は縦に揃っています。ピッキング側は傾斜で下の段ほど手前に出ているので、作業効率を向上させます。保管するときは、順次押し込んでいくタイプです。
・冷凍・冷蔵対応自動倉庫
常に保管温度や湿度をコントロールして、保管物の品質や鮮度を管理するタイプ。冷蔵系の倉庫内では、人間の作業時間が限られているため、低温物流の分野でこのタイプを使用します。
(左:傾斜式流動ラック 右:冷凍・冷蔵対応自動倉庫)
お客様事例インタビュー
株式会社ニデック様は、1971年の創業以来、「見えないものを見えるようにしたい」、「見えたものを認識できるようにしたい」、「眼に関する優れた機器を作りたい」という想いのもと、医療、眼鏡機器、コーティングの3つの分野に事業を展開している会社様です。
・自動倉庫導入前に感じていた課題
・実際に導入して解決できたこと
・今後の展望
について、株式会社ニデックの菊池様にお話を伺いました。
――解決したかった課題について教えてください。
・在庫管理
このままいくと収納するところがパンパンになっちゃって、たぶん業務が破綻するだろうなという危機感があったんです。例えば、眼鏡屋さん向けのテーブルが平積みで並べてあって、縦積みが出来ない状態でした。スペースが大量に必要になっていて、運搬の費用・工数が掛かっていました。
このテーブル製品は、作るのに結構時間がかかるので、ある程度オーダーを出しておいて在庫をストックしています。そして注文が入ったらすぐ組み立てて調整して、2、3日で出すようにしていました。この一つの機種で海外、国外、右利き左利きで4種類と、さらに色が3種類あるので、在庫が持ちきれなくなってしまいました。
あとは、誰でも簡単にボタンを押せば先入れ先出しを考慮したロットが出てくることをやりたかったです。コンピューターに任せちゃえば欲しいものがすぐ出てくるような。
・運搬の工数
部品や製品の保管倉庫が点在していたんですけど、それを管理するのに色々と工数が掛かっていたんです。どこかに大きい倉庫を借りて一つで管理するにしても、管理工数が掛からないにしても、運搬の工数がかかるので、ニデック内で敷地を有効活用して大量に保管できる倉庫が欲しいなと。
――自動倉庫導入前の運用方法を教えてください。
ニデックにはトラックがあるんですけど、部品管理課にはトラックがないので「トラックを何時から貸してください」と毎日言って、外部の倉庫に取りに行く作業を一日に1回~2回、毎日やっていました。1回行くのに30分くらいかかるので、その移動の時間がすごく無駄だったんですよね。
あと、システム的に管理されていないので、前回保管した人と違う人が行くと、どこからどう出していいのかさっぱり分からないんです。だから必ず持って行った人が出しに行かないと、どんな順番で収納しているかわからないので、勘やコツがいる仕事でしたね。
――計画から本稼働までについて教えてください。
2019年の9月くらいまでに企画書を作って、承認をもらったのが11月の終わりです。結構早く建ちました。本稼働は4月とアナウンスしていて、3か月くらい余裕があったので、それまでに倉庫に入ってどういうことができるのかなって試しにやったりしていました。
――弊社へ声をかけていただいたきっかけはなんでしょうか。
トヨコンさんにも倉庫を借りていましたし、物流に関することの総合的な会社だと思っています。梱包作業場がすぐ隣で一番身近だったので、なんかないですか?という軽い感じで声をかけて、そこから乾さんを紹介していただいた形ですね。
――自動倉庫の操作方法
QRコードをピっとスキャンすれば、品番とロット番号がセットされます。QRコードに数量のデータはないので、手で入力してボタンを押せば、空いたパレットが下りてきます。そのパレットに製品を載せて、またボタンを押せば戻っていきます。
――ロケーション管理
「何が何個どこにあるよ」っていう情報は、大元の基幹システムの方で全部把握しています。私たちとしては、下りてきたパレットに載せてボタンを押せば、後はシステムが勝手に空いているところに収納してくれているという認識でいます。
何か一個欲しいとなった時には品番と数量を入れれば、自動で出てきて一個だけ取って、ポンとボタンを押せば数量もシステム上で変えてくれます。
――導入後の効果について教えてください。
●物流品質の向上
自動倉庫によって、誰がやっても確実に先入れ先出しができるようになりました。
●業務負荷軽減、本来の業務に集中できる
フォークリフトの免許を持った正社員が本来の業務に専念できるようになりました。今までだったら、ハンドリフトでここに収納したい、でもここに収納すると、こっちが空かなくなってしまうから、横にずらしてからスペースを空けて収納するとかやっていました。でもそういうことを一切考えずに、ただ下りてきたパレットの上にものを置いて、ボタンを押すだけで良くなりました。
●外部スペースのコストとリスクの低減
2021年6月末までには、外部で借りている3つの倉庫がなくなるんです。そもそもプロジェクトが立ち上がってからの目的に、
・運搬をなくす
・誰がやっても簡単に出せる
・外部倉庫をなくす
がありました。いま毎月外部倉庫で管理費がかかっていますけど、それをやめて、キャッシュフローをよくするということがありました。
この3つを目標としていたので、それが今のところはすべてクリアできていると思っています。
――今後の展望について教えてください。
現状、倉庫内でエラーが出てしまうと、中に入れるのがクレーン特別教育をした者だけなんです。今ニデック内では2人しかいないんですよね。今後、特別教育をどんどん取りながら誰でも入れるようにしたいです。
次のタスクが「効果の測定」になっているんです。その目途となるものが、入出庫を月に301回自動倉庫でできれば、工数的にペイができるんです。12年でペイができるようにやっているんですけど、4月は260回くらいの入出庫なので、もう少し稼働を上げたいなと思っています。
今後稼働を上げるには、対象を増やすとか、出ない製品を違う倉庫に送って、出る製品を自動倉庫に入れるとか、そういうことをやっていくつもりです。その辺は様子を見ながら稼働を上げていきたいなと思っています。
自動倉庫のメリット・デメリット
まず、乾氏は自動倉庫の「メリット」を3つ挙げています。
1.人手による受け入れ、出庫作業を効率化
今まで人間がおこなっていた入出庫やピッキング作業などの倉庫内業務を自動化することで、従業員の負担や安全性が向上。また、ロボットは24時間稼働することができるので、生産性が上がり、従業員は長時間作業やわずらわしい交代制に対応する必要がなくなる。
2.省スペースの実現
倉庫内の人の手が届かないような高さ方向のスペースも有効活用できるので、今までの保管スペースを削減することが可能になる。
3.ヒューマンエラーの削減
ニデック様のインタビューにあったように、ベテラン社員の勘やコツが必要な先入れ先出しも自動でシステムが行ってくれるため、ヒューマンエラーの削減や保管製品の把握、業務経験などの従業員育成の時間まで削減することが可能になる。
次に、一方の「デメリット」を3つ挙げています。
1.導入コストが高い
システムは便利な反面、イニシャルコストが大きい。しかし、現状かかっている人件費や諸費用を明確化し、自動倉庫を導入した際に削減できるコストとの差額比較で解消できる。長期的な視点で見て、価値をどこに置くかが重要。
2.保管方法が固定される
ニデック様インタビューにもあったように、自動倉庫の種類によっては、保管方法がある程度固定されるため、荷姿の再検討や保管形態の変更が必要になる場合がある。
3.在庫量変動やトラブル時の対応
取り扱う商品や製品によって、季節ごとに在庫量が変動する場合には、保管方法や保管場所の変更などの対応が必要になる。トラブル時のマニュアルをしっかり構築するだけでなく、十分なシステムサポートを提供してくれる企業を選定する必要がある。
まとめ
最後に、自動倉庫導入により、改善可能な課題についてまとめます。
・段積みできない在庫スペースの削減
天井高くまで設置された高層ラックに保管することで省スペースになる。
・受入、出荷作業を効率化
ボタン操作でロケーションを管理できる。
・先入れ先出しの徹底を実現
ヒューマンエラーを削減し、誰が行っても先入れ先出しが確実にできるようになる。
自動倉庫は、保管したい物によって適しているタイプや保管方法が異なってくるため、それぞれ選ぶ必要があります。そして、保管業務の負担を軽減させながら、課題解決のために考えた施策が、倉庫で遂行しきれる状態をつくることが重要になってきます。
業務の効率UP、または自動化に向けて、省人化機器の導入を検討されていますか?
トヨコンの省人化機器サービスをこちらで紹介しています。ぜひご覧ください。
ご相談、お問い合わせはお気軽にどうぞ!