ピッキング作業を改善するには―物流倉庫の生産性を高めるポイント
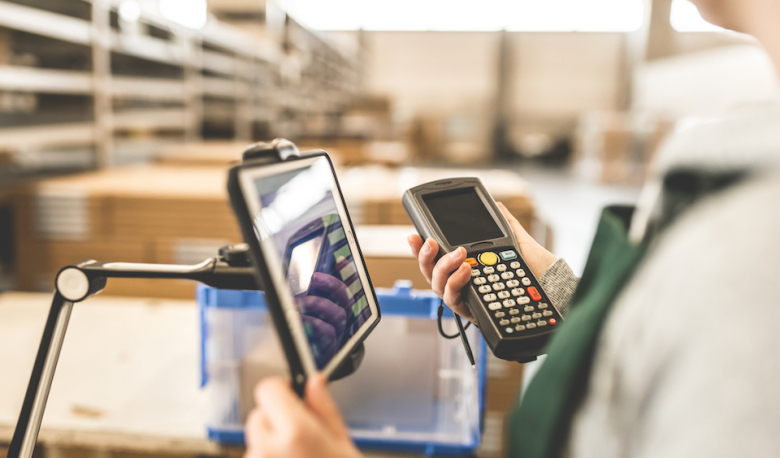
物流倉庫の業務のなかで、多くのリソースが投入されている作業はピッキング作業といえるのではないでしょうか。
多くの作業者が倉庫内を往復しながら商品を集めて回るピッキング作業は、改善により大きく生産性を向上させることができる可能性があります。ピッキング作業の代表的な課題と効率化のポイントをご紹介します。
ピッキング作業の課題
物流倉庫の稼働生産性を高めるうえで、最も重要といわれるのが、ピッキング作業です。ピッキング作業は庫内作業全般のなかでも自動化が難しく、人の手による作業が大きな割合を占めるため、改善の余地が多く残されている場合があります。ピッキング作業における課題として代表的なものは次の3つです。
商品を探すのに時間がかかっている
ピッキングは商品の場所に直行できる状態にあるのが理想です。しかしそうではない場合、つまり商品を探すのに時間がかかるケースでは次のような理由が考えられます。
- すでに品切れとなっているが、未補充の商品を何度か探している
- ピッキング指示書に、商品を探すために必要な情報が不足している
- 商品を探すにあたり、手間が発生するピッキング確認項目がある
取り出しに時間がかかっている
商品の場所へたどり着いた後、その商品をすぐに取り出せる状態になければ効率よく作業できません。そういった非効率を生んでいる理由には、次のような状態になっていることが考えられます。
- 商品を1個単位で取り出すまでに、箱の開封や梱包材の処理など別の作業がある
- ケースの開口部が作業者側を向いていない・棚のどこかに引っかかるなど、ケースから商品を取り出しにくい
移動の時間が長い
倉庫が広ければ広いほど、ピッキング作業全体に占める移動時間の割合は大きくなります。このことから、移動時間の短縮が、ピッキング作業を大きく効率化するための重要なポイントと考えることができます。しかし、作業者を急がせるような方法は解決策とはいえません。それでは焦るがゆえの事故につながったりと、逆に非効率を生み出す可能性もあることでしょう。移動時間を短くするためには、次のような問題を仕組みの面から解決する必要があります。
- 棚の配置が悪く、回り込まなければたどり着けない場所がある
- 通路が狭いため、作業者やカートが同時に通れない
ピッキング作業効率化のポイント
それではここで、効率化され生産性の高いピッキング作業とはどのようなものかを考えてみましょう。必要な条件は大きく次の2点になります。
- ピッキング作業の稼働率が高い
- ピッキング作業のための環境が整っている
このような理想的で高効率なピッキング作業を実現するためには、作業の仕組みと作業場所の条件を次のような状態に近づけることが必要です。
- ピッキング作業者の前に常に商品がある
- わかりやすいピッキング指示書が、常に最新の状態で目の前にある
- 商品を集める容器が、効率的に切り替えられる
- 前工程・後工程とのバランスが取れていて、手待ちが発生しない
これらを一度にすべて実現するには、大規模な改善が必要になることもあります。しかし、ひとつずつでも改善できれば、ピッキング作業は効率化されます。
ピッキング作業の具体的な改善事例
ピッキング作業の効率化に成功した事例を見てみましょう。なかにはすぐにできる方法もあります。
品出し方法の変更
商品の置き方だけでも、ピッキング作業を効率化することはできます。例えば、品出し作業の際に、ケースを開口しておく、作業者側に向けて置くことで、その後のピッキング作業は効率化されます。品出し作業は工数が増えますが、その分ピッキング作業の工数は減ります。例えば、20個入りのケースであれば品出し作業の工数はプラス1、ピッキング作業の工数はマイナス20となります。このように全体のバランスを考え、ピッキング作業の稼働率に焦点を合わせた工夫をするだけでも効率化は可能です。
マテハン機器の導入
マテハン機器の導入により、ピッキング作業を効率化する方法もあります。ハンディターミナルや無線表示器などによって、ピッキング作業に必要な情報を確認し、確実性を増して効率性を高めることができます。また、ソーターのように作業者の移動時間を削減する機器もあります。
マテハン機器の利点についてはこちらの記事もご参照ください。 →「物流業務省力化の強い味方「マテハン機器」って何?」
副資材の使い方を見直し
一見あまり関係ないように思える副資材の使い方も工夫することで、ピッキング作業がスムーズに進むことがあります。
作業者が商品を集めるためのケースは、常に更新されるようにすることで、直接的にピッキング作業を効率化します。また、ピッキング作業に梱包作業が付随する場合、作業性の高い緩衝材を使ったり、緩衝材の置き場所を工夫したりすることで、作業は大きく改善されます。
梱包作業は別工程であり、別の作業者が担当するという場合でも、その工程が詰まってしまっていては、ピッキング作業上、後工程の処理待ちが発生する可能性があります。製函機や自動梱包機などを導入することにより、前工程・後工程を効率化し処理待ちを排除するのも、ピッキング作業の効率化に必要な場合があります。
管理システムの導入
物流の管理システムを導入すると、多くの場合ピッキング作業も効率化されます。物流センター管理システムや在庫管理システムなどがその代表例です。
作業者に的確な指示を出し、ピッキング作業の状況が瞬時に反映、共有されるため、時間差が原因で起こるズレやミスがなくなります。また、商品の場所を視覚的に表示するようなシステムでは、探す時間と移動時間を短縮でき、ピッキング作業の効率が直接向上します。
在庫配置の工夫
近年では、AIにより在庫の配置を最適化するシステムも登場しています。ピッキングと出荷に関する作業実績データをAIが分析し、最適な商品配置を割り出してくれるのです。
このシステムでは、ピッキング頻度が高いものを近くに、出荷頻度の高い商品をバラして配置するといった、効率的な商品配置が導かれます。それだけでなく、ピッキング作業時間を短縮するために、棚の上中下のどの段に置くべきかといった細かい部分まで見つけてくれるのです。
こうしてシステムから出された配置替え作業リストに従い商品を配置することで、ピッキング作業の効率が16%向上したという実績もあります。
ピッキング作業の改善が全体の生産性を押し上げる
ピッキング作業を効率化するために必要な要件、効率化のための具体例をご紹介しました。マニュアルワークが多いピッキング作業は自動化が難しいといわれますが、課題を洗い出し、作業を細分化して考えることで、自動化できる部分が見えてきます。また、簡単なレイアウト変更により大幅な効率向上につながったり、少ない投資で大きな効果が得られたりする場合もあるのです。もう一度、ピッキング作業で改善できる部分がないか、考え直してみてはいかがでしょうか。
倉庫の確保、倉庫業務のアウトソーシングを検討されていますか?
トヨコンの倉庫管理サービスをこちらで紹介しています。ぜひご覧ください。
ご相談、お問い合わせはお気軽にどうぞ!
参考:
- 人工知能を活用して継続的な業務改善を図る「Hitachi AI Technology/倉庫業務効率化サービス」を提供開始(PDF)|日立製作所
- ピッキング|ミスター物流
- (編集者註:倉庫内作業を効率的に行うための6つのポイントとは?|アトムエンジニアリングは現在リンク切れ)
- (編集者註:自動包装システム|佐川グローバルロジスティクスは現在リンク切れ)